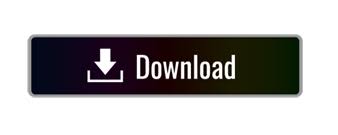
Looking at the output it may not be immediately clear why you’d ever choose the flat version. The image below shows a 3D part on the left and a prismatic part on the right. 2D toolpaths are used almost exclusively to machine parts that are prismatic– that is, all of the surfaces of the part are horizontal or vertical.ģD toolpaths are used to machine parts that are more freeform- they may have not have any perfectly vertical or horizontal surfaces. The first thing to discus are the ways 3D toolpaths differ from 2D toolpaths. We’ll also simulate some toolpaths using the excellent Cutviewer CNC simulator. We’ll do the latter and try to gain an intuitive understanding of the concepts involved. There are a couple of ways to approach this question- the boring mathematical approach or just show some pictures and try to point out the characteristics of various toolpaths. In a roundabout way, that leads into another common support question- “Why are there so many toolpath types and which one do I pick?”
#CUTVIEWER MILL SOFTWARE#
The last post I wrote here covered a common support question I get for the CNC Software (MeshCAM) that I develop- “How to choose a stepover value”. If you’ve never tried MeshCAM, give it a shot. He’s gone out of his way to create super simple user interfaces that ensure his users succeed in their CNC projects. In fact, that’s one of the great strengths of his software too. Robert’s forte, aside from creating wonderful software like MeshCAM, is making very complex topics easy to understand. Please welcome Robert Grzesek, founder of GRZSoftware and author of MeshCAM 3d cnc cam software for this guest post on the fundamentals of 3D milling toolpaths in CAM.
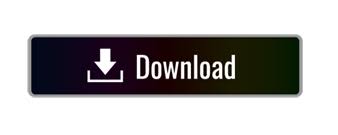